Inauguração da linha de montagem do Gripen no Brasil: o que ainda não contaram para você (parte 2)
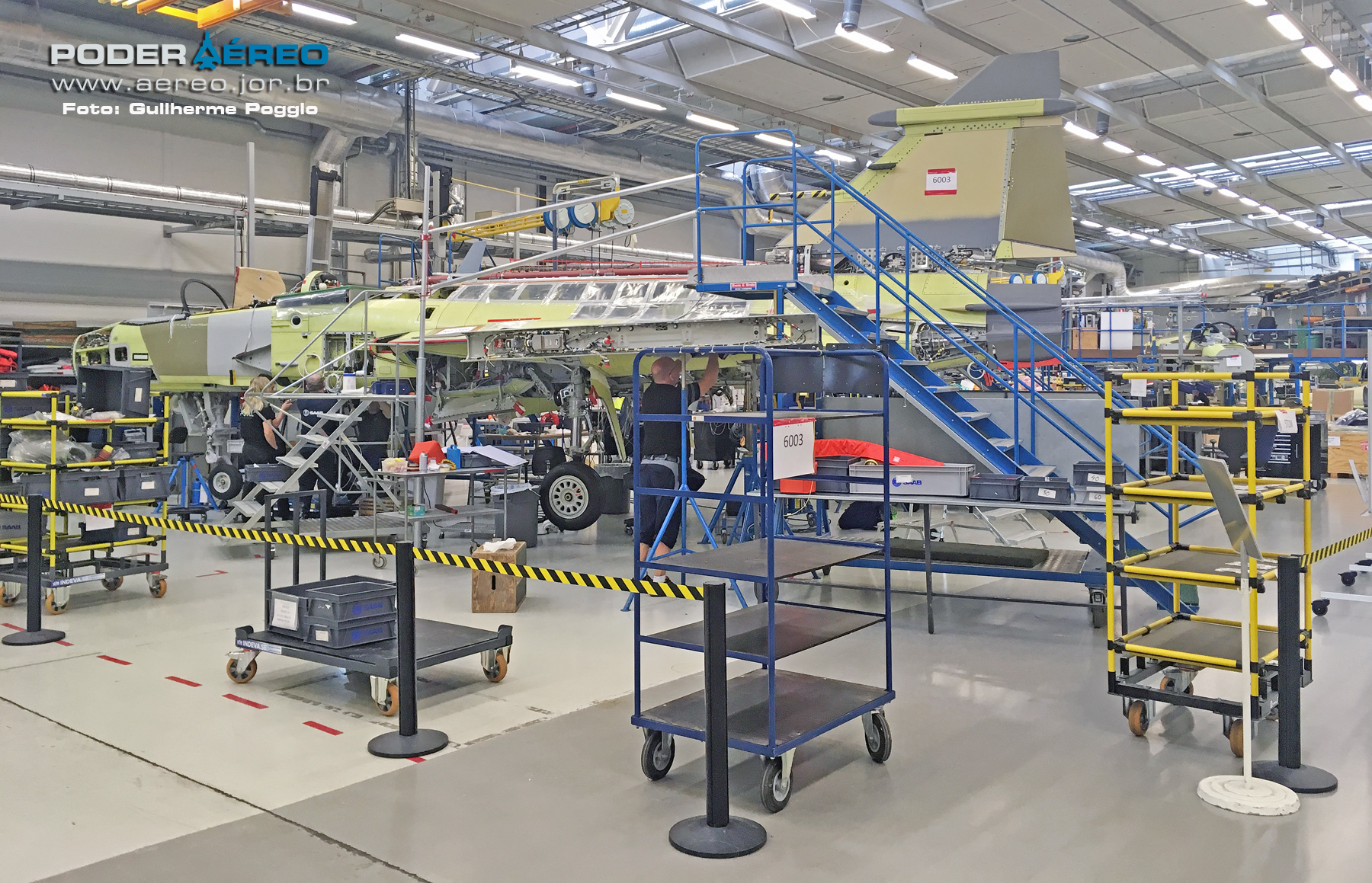
Por Guilherme Poggio
PROCESSO INDUSTRIAL
Antes de entrarmos nos detalhes específicos da linha de montagem do Gripen, recém-inaugurada no Brasil, vamos descrever como essa atividade ocorre na Suécia. O Poder Aéreo teve a oportunidade de conhecer todo o processo de montagem final na fábrica da Saab em Linköping (Suécia) em setembro de 2019.
O nascimento de um Gripen já foi narrado aqui no Poder Aéreo em diversas matérias, mostrando como são fabricadas as peças iniciais tanto no Brasil, na SAM (Saab Aeronáutica Montagens, em São Bernardo do Campo / SP ) como na Suécia. Neste link você acessa uma ótima matéria do editor Fernando “Nunão” sobre a fabricação e montagem das aeroestruturas, tendo ao final dela uma série de outros links para matérias anteriores relacionadas ao tema.
Passada a etapa de fabricação individual dessas grandes estruturas (como as asas, a fuselagem central, a fuselagem dianteira e traseira), tanto na Suécia quanto no Brasil, elas são todas remetidas à linha de montagem final e unidas numa etapa que se chama “montagem estrutural” (structure assembly). E assim a célula começa a tomar a forma de um caça.
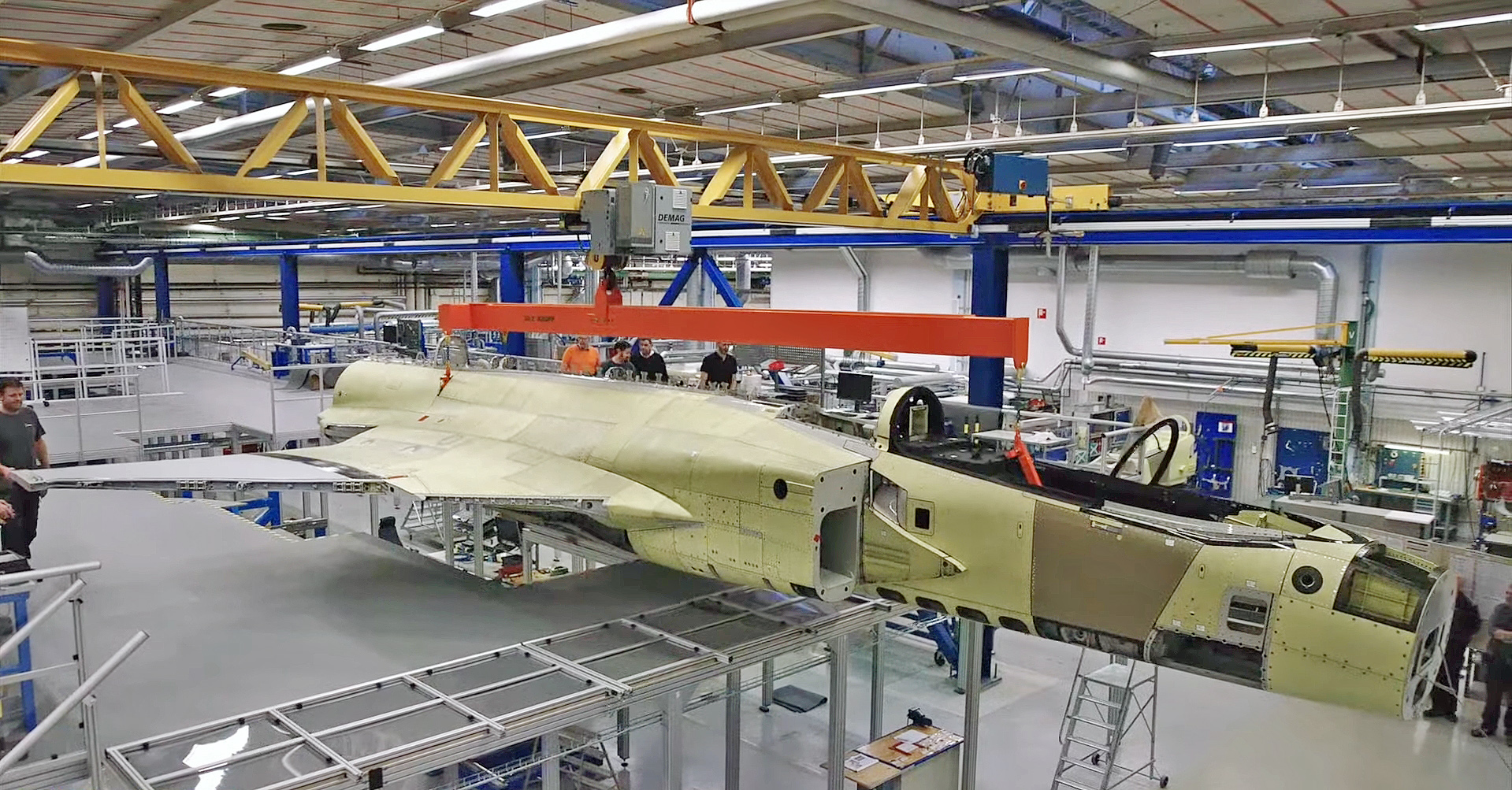
Quando a célula chega à linha de montagem final (final assembly) ela é apenas um “esqueleto” metálico, com suas partes estruturais e painéis cobertos pelo “primer” (elemento que que dá o aspecto amarelado que tem a função de proteger o alumínio aeronáutico da corrosão e preparar a superfície para receber a pintura final). Também se pode ver algumas partes fabricadas em material composto (geralmente na cor cinza). A célula ainda está completamente vazia e pesa aproximadamente três toneladas, o que é menos da metade do peso final da aeronave (vale lembrar que o peso vazio de um Gripen E monoposto é de aproximadamente oito toneladas).
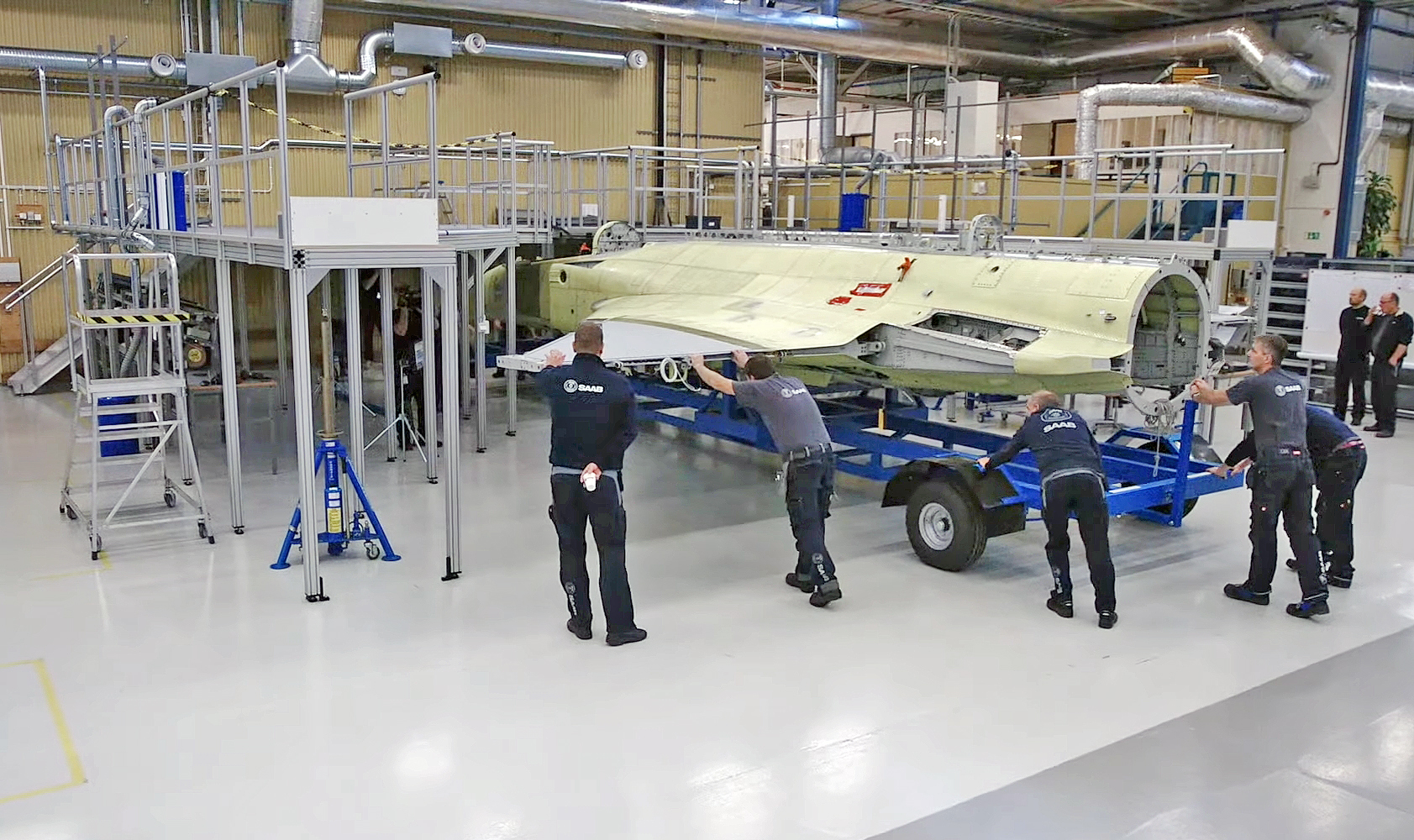
Toda a célula vazia que chega à linha de montagem final passa por três etapas (ver imagem abaixo). Na primeira, a estação 1, ela é “abraçada” pela bancada. Neste local o “esqueleto metálico” (imagens acima) recebe suas “veias e artérias”: quilômetros e mais quilômetros de cabos e dezenas de metros de redes / tubulação (combustível, fluido hidráulico, etc.). Além disso, outros componentes de grande porte como a deriva e o trem de pouso são incorporados à estrutura, totalizando cerca de 17.000 itens. Esta é, de longe, a maior de todas as estações.
É importante destacar que a montagem é executada sem que um único documento, instrução ou manual físico, em papel, tenha que ser consultado. Trata-se do conceito da “fábrica sem papéis” (paperless). Os desenhos e especificações estão todos em formato digital (imagem abaixo), constituindo imagens tridimensionais em que se pode destacar cada pequena parte. Caso um processo ou um desenho tenha que ser atualizado, a mudança é rapidamente enviada para todas as estações da fábrica e até mesmo entre as fábricas, seja no Brasil, seja na Suécia. O mesmo vale para a já mencionada fábrica de aeroestruturas de São Bernardo do Campo.
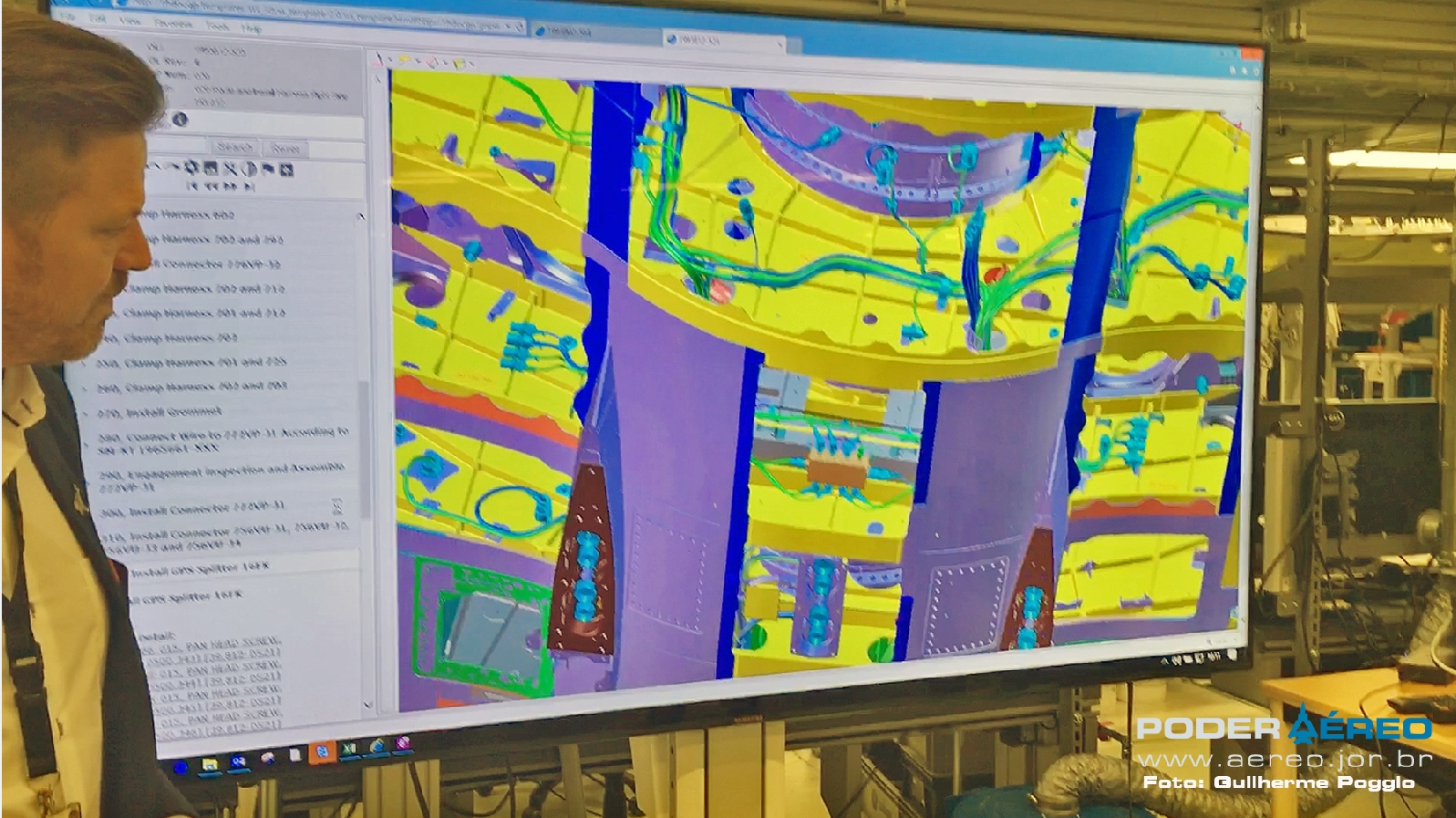
A partir desse ponto a aeronave segue para a próxima estação (2) e já está preparada para receber diversos itens de hardware, como computadores, aviônicos diversos e outros equipamentos da cabine (incluindo o painel). É também nesta estação que receberá o APU (sistema auxiliar de energia), o motor, os canards móveis e o radar. A partir da estação 2 a aeronave não precisa mais das bancadas.
Um ponto interessante na linha de montagem final sueca é presença de um único engenheiro de qualidade responsável pelo andamento de todo o processo. Os funcionários da montagem (operators) são totalmente responsáveis pela qualidade do serviço que entregam (self-authority inspection). Trabalhando desta maneira o engenheiro responsável pela linha de montagem final disse que a Saab atingiu níveis mais altos de qualidade e melhores resultados de forma geral. Esta nova forma de trabalhar estava na lista de itens da Saab a serem transferidos para a indústria brasileira.
Por fim, na estação 3, ocorre a verificação dos componentes finais. Essa etapa é seguida do carregamento da parte lógica da aeronave (os softwares). Com tudo montado e instalado, o sistema como um todo é testado de forma simulada no solo. Na imagem abaixo vemos o primeiro Gripen E da Força Aérea Sueca já totalmente montado e passando por diversos testes antes de deixar a linha de montagem final.
Ao deixar a porta da linha de montagem final, o caça segue para a oficina de pintura, onde recebe o revestimento definitivo. Agora o novo exemplar do Gripen está quase pronto para voar. Quase, porque ele ainda não possui o assento ejetável. Como o sistema de ejeção possui elementos explosivos (o propelente do foguete que impulsiona o assento para fora da aeronave em frações de segundo), este componente é instalado em local apropriado por questões de segurança.
Antes que a aeronave realize qualquer voo é feita a checagem no sistema de armazenamento de combustível. Todos os tanques são enchidos e verifica-se a comunicação entre os mesmos. Com a integridade do sistema de abastecimento conferida, o novo caça segue para o teste de motor. Se tudo estiver ok, o jato fica disponível para o seu primeiro voo. A partir daí, caso os testes de aceitação (no solo e em voo) estejam em conformidade com as especificações do cliente, é feita a entrega da aeronave. Todas estas etapas pós-linha de montagem final também deverão ser feitas pelos caças que serão construídos na recém-inaugurada linha da Embraer.
continua na parte 3…
Clique nos links para acessar a parte 1 e a parte 3 desta matéria.
Alguém saberia dizer a marca e modelo da APU do GRIPEN?
Pelo que sei é da Hamilton Sundstrand, uma subsidiária da UTC (a mesma que fabrica o Black Hawk e outros helicópteros). E esse APU é usado nos E-99 também (com pequenas modificações).
Muito obrigado
Em temos de marcas e fabricantes o mundo já foi bem mais eclético rsrsrs
Hamilton SundstrandOrigem: Wikipédia, a enciclopédia livre.
Hamilton Sundstrand
A Hamilton Sundstrand foi uma corporação americana atuando a nível mundial que produzia e efetuava a manutenção de produtos industriais e aeroespaciais para o mercado global. Uma subsidiária da United Technologies Corporation, tinha sua sede em Windsor Locks, Connecticut. A compania foi constituída a partir da fusão da Hamilton Standard com a Sundstrand Corporation em 1999. Em 2012, a Hamilton Sundstrand foi fundida com a Goodrich Corporation para formar a UTC Aerospace Systems.
Em 2018, a UTC Aerospace Systems e a Rockwell Collins se juntaram para formar a Collins Aerospace.
Post bem esclarecedor,Parabéns !!!!
Ficou bem claro que não é como montar aquele móvel da cozinha como muitos acham. Trem de pouso é na parte 1 ou na 2?
A resposta está na matéria colega é só ler..
Tipo o meu irmão inconformado ao saber que um avião deste não era fabricado em 1 semana ou menos e sim em meses e até anos.
Caramba, 35 km de cabos…
Muito legal sua matéria, Poggio. Parabéns!
Aguardando parte 3
“fábrica sem papéis” (paperless). Os desenhos e especificações estão todos em formato digital (imagem abaixo), constituindo imagens tridimensionais em que se pode destacar cada pequena parte.
A Embraer tem investido alto em digitalização de projeto, linha de montagem e serviços de manutenção.
Os projetos já são digitais há muitos anos. No entanto ainda reina a produção de “documentos para a construção”, ou seja a geração de documentos convencionais a partir do 3D para guiar a construção. A novidade é olhar direto para o modelo, ao invés de ficar buscando os “PDFs”, que ainda correm o risco de estarem desatualizados.
Sim, uma vantagem do sistema é a atualização simultânea do projeto.
Por exemplo, a mesma mudança será atualizada e visualizada ao mesmo tempo por um técnico ou engenheiro consultando a tela de computador na linha de produção de aeroestruturas da Saab Aeronáutica Montagens, em São Bernardo do Campo-SP, ou na fábrica da Saab em Linkoping, na Suécia, ou no GDDN (Gripen Design and Development Network – Centro de Projetos e Desenvolvimento do Gripen) em Gavião Peixoto, ou na linha de montagem final do Gripen no hangar G-1350 da Embraer, também em Gavião Peixoto / SP
Olá Nunão, no começo dos anos 90, antes de ingressar na universidade, trabalhei em uma grande construtora. Todo o projeto era em papel. Lembro de pedir um computador para gerenciar as planilhas de materiais… nunca tive uma resposta do escritório central. Lembro de ter feito um estágio em 1989 em um escritório que projetava cozinhas industriais. Eles já usam CAD. Era algo muito avançado, mas os projetos de arquitetura das casas era tudo feito em papel. Fiz muto projeto para a prefeitura em papel vegetal.
Eu comecei minha carreira em propaganda na virada dos 80-90 ainda num ambiente analógico em que se fazia layout com ilustrações à mão, colagem de tipos para as chamadas, e criando texto com caneta e papel para depois anexar ao layout, já datilografado. Felizmente (e infelizmente também) o computador já estava chegando ao ambiente de criação publicitária – já estava no ambiente de produção – fazendo os layouts ficarem híbridos, e em seguida serem produzidos de forma totalmente digital, para impressão em alta qualidade e mais tarde apresentados em telas grandes. Facilitou muito o trabalho, abriu muito mais possibilidades e… Read more »
Nesse momento em que vemos a linha de produção do Gripen sendo inaugurada na Embraer, é que fica claro porque a Aeronáutica o escolheu. Se fosse o F-18 dos EUA, provavelmente já estaríamos com as 36 aeronaves operacionais, porém ficaríamos sem a transferência de tecnologia e 100% dependentes. Se fosse o Rafale, é possível que houvesse alguma transferência de tecnologia, a exemplo do programa de construção de submarinos, porém os custos de operação e manutenção desse caça são mais altos que os do Gripen. Num futuro não muito distante, estaremos fabricando nossos próprios Gripen.
“Se fosse o F-18 dos EUA, provavelmente já estaríamos com as 36 aeronaves operacionais…”
Tem um pequeno entrave aí, que também está atingindo o Gripen: realizar os pagamentos em dia e na quantidade acordada. O Gripen só está atrasando dessa forma pq a FAB não está cumprindo o calendário de pagamentos acordado, então é razoável prever que tbem não estariam fazendo com o F-18, portanto, sem entregas no prazo.
Eu sei que ainda não são pagamentos dos aviões em si, mas sim de coisas acessórias.
Até onde eu me lembro, os pagamentos vão ser iniciados após a última entrega do primeiro lote.
Leandro,
Isso era o proposto pela Saab em sua oferta que ganhou o F-X2.
Porém, na negociação até a assinatura do contrato de financiamento, houve mudanças na carência para redução de juros, inclusão de outros itens etc, como em qualquer negociação de contrato.
Você pode ver mais detalhes nos relatórios de gestão da FAB a partir de 2015. Tem no site da FAB, ainda deve estar numa seção chamada transparência, se não me engano.
Olá Leandro. Isso era uma proposta inicial. Quando foram negociadas as condições do empréstimo, o Tesouro conseguiu reduzir as taxas de juros mas também reduziu a carência. O Brasil já vem pagando as parcelas do financiamento externo pelo menos desde a entrega do 4100. A conta tem sido da ordem de R$ 1,5 bilhão por ano. Creio que em reais, o programa deve custar cerca de R$ 22 bilhões. Creio que já foi pago mais da metade do financiamento.
Camargo e Nunão, obrigado pelas infos. Acho que vou dar uma olhada nos relatórios de gestão da FAB, mas o cenário vocês me passaram.
Caro Dam. O Tesouro tem feito os pagamentos dentro do prazo do contrato. Este contrato já recebeu vários aditivos, algo comum em um programa da ordem de 20 bilhões de reais. Anualmente, são pagos cerca de R$ 1,5 bilhão. Pelo que lembro, os pagamentos são semestrais. Já foram pagos mais da metade do financiamento.
Você esqueceu que a Pandemia parou tudo em quase 2 anos!!
Mais uma excelente matéria do Poggio, com conteúdo apurado em visitas tanto à linha de montagem na Suécia quanto à nova no Brasil. E não basta visitar, precisa que o visitante tenha o olhar atento (e crítico) para enxergar o que nem sempre está óbvio e fazer as perguntas que gerem informações de verdade.
Parabens ao poder aereo pela matéria!
Importante dizer que o sistema de manufatura da Embraer já é paperless em suas linhas de montagem já fazem alguns anos.
Quanto ao tempo para se produzir uma aeronave, ele varia bastante… Alguns poucos meses, e isso considerando todo o processo.
A Embraer já chegou a produzir 200 aeronaves-ano, considerando apenas os modelos comerciais e executivos.
Os “operators” são tão responsáveis pela qualidade quanto o engenheiro da área. Isso mostra o quanto a empresa precisa de gente altamente comprometida com o profissionalismo e qualificada na área.
Participar da produção de uma aeronave, por si só, já deve exigir do trabalhador um nível de responsabilidade com o seu ofício enorme; imagine então de uma aeronave de altíssimo desempenho.
Esta nova forma de trabalhar estava na lista de itens da Saab a serem transferidos para a indústria brasileira.´´
Imagino que esse item em específico interessava muito a Embraer…
Ia perguntar sobre a colocação do canhão orgânico, sistemas de chaf e flares e do IRIST, mas imagino que essa resposta esteja na parte 3.
No mais, muito obrigado aos editores pela matéria.
Willber Rodrigues, a aeronave já sai dessa linha praticamente pronta. E isso inclui a montagem do canhão interno e dos suportes para chaffs entre outros.
Não, esta maneira de trabalho, esta tecnologia paperless, o montador qualificado que não requer um inspetor, e etc já são processos e tecnologias de uso comum e a muito tempo em uso na Embraer.
Oi. Femb. De fato, o projeto do KC390 foi tido feito de mofo digital e usando simulação 3D. Fiquei impressionado com o vídeo da produção do F35 que usa a projeção de informações na fuselagem para auxiliar o funcionário.
Já vi isso por aqui também. Além de muitas outras tecnologias usadas na montagem.
Esse caça é muito top.
Se eu fosse um bilionário eu iria tentar comprar um para deixar numa pista de pouso particular em uma grande fazenda no interior do país.
Pilotar um desses, mesmo que esteja sem armamentos, seria um sonho.
Olá Colegas. Segundo o Relatório da FAB, o programa FX2 tem os seguints valores: $ 39 bilhões de coroas suecas, $ 245 milhões de dólares e $ 185 milhões de libras. O Tesouro assinou um contrato com um banco sueco para financiar o programa no valor de $ 39 bilhões de coroas e $ 245 milhões de dólares, que foi assinado em 15 de agosto de 2015. O Tesouro começou a pagar o financiamento em 2015, portanto não teve carência. Até 2022, o Tesouro já havia pago $ 22 bilhões de coroas, $ 97 milhões de dólares e $ 36… Read more »
Ahhh. Os pagamentos estão programados até 2028, quando o financiamento terá sido 100% quitado. É isso também.
Então,
Pelo que entendi, isso (2028) é a previsão de uso do valor total financiado, a ser recebido do banco sueco. Ou seja, o dinheiro que mantém o projeto andando.
As parcelas dos pagamentos do principal continuarão pelos anos seguintes.
Camargoer, Talvez (repito, talvez) você esteja confundindo pagamentos para execução física do contrato, a partir dos valores recebidos do banco financiador, com pagamentos do financiamento do contrato, feitos para o banco. O contrato continua tendo carência dos pagamentos / amortização do principal. Inicialmente era 2025, não sei exatamente como mudou com os aditivos desde a assinatura. Para isso tem que olhar todos os relatórios, ano a ano, coisa que eu fiz anos atrás, deixei algumas anotações num word para uma matéria a respeito (nos moldes da que escrevi para a Tamandaré), mas nem acho mais porque não tive tempo pra… Read more »
Olá Nunão. Obrigado. Você talvez (e digo talvez) tenha razão. Lembro que no documento do Senado falava em pagamentos semestrais para o banco. Os valores que coloquei aqui são aqueles colocados no relatório da FAB de 2022. Talvez algum outro colega possa nos ajudar a garimpar os dados. Depois de 9 aditivos no contrato de financiamento, nada do que foi será do jeito que já foi um dia
Parabéns ao autor das matérias, se encontram bem didáticas e elucidativas…
Sobre o paperless imagino como deve ser feito o backup de dados, informações, desenhos […] e a segurança cibernética de tudo isso. Certamente há tentativas de burlar esta última.
André,
Se não me engano, a conexão é própria da Saab, não é pela Internet comum.
Obrigado, Nunão.
E pensar que sobravam críticos ao projeto, que defendiam com unhas e dentes a proposta americana, sem nenhuma transferência de tecnologia! Fico pensando, como é possível termos “brasileiros” que defendem a contínua subserviência, especialmente tecnológica, do Brasil, e que conseguem dormir tranquilamente à noite.